Challenges of strength and durability analysis
- Alvaro Filho
- Jun 4, 2024
- 4 min read

Accurately predicting strength and durability is crucial, especially in electric vehicles, where heavy batteries alter mass distribution and create new charges. As engineers, we seek a balance between durable components, cost and material weight.
During this process, we deal with large amounts of data from various sources. However, do we know how to integrate them efficiently? Despite a lot of information, we may not know which fatigue analysis method is most suitable.
Test results, often represented by stress values in color images after inputting loads, geometry and material data, are not always clear about the strength and fatigue of the structure.
CAE Fatigue Methodology for Design Optimization and Virtual Validation
Using CAE Fatigue Methodology for Design Optimization and Virtual Validation
There is a significant difference between how loads and events affect the structure as a whole and individual components. Even after long analysis processes, it may be necessary to identify which events and loads contribute to the damage.
Common Challenges:
Loads on the Structure: Multiple loads act on a car, such as the independent excitation of each wheel by the road, creating multiaxial loading situations. External influences such as temperature and oxidation must also be considered. How do you get and measure these loads?
Stresses and Strains: To understand fatigue, it is crucial to know the stresses and strains in the structure. How do you transform measured or simulated loads and local geometry into stresses and strains that affect the structure?
Effect of Manufacturing Process: The manufacturing process can change the basic fatigue properties of the material. Surface finishes or welding during assembly create residual stresses that influence the behavior of the material. Do your experiments consider all of these influences?
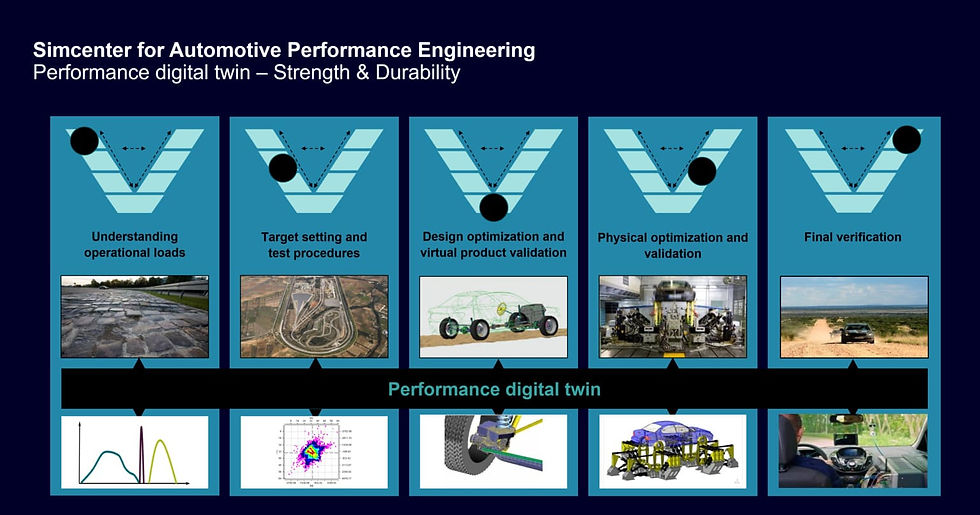
A process of resistance and durability from end to end.
CAE Fatigue Methodology for Optimization and Validation
Simple but comprehensive. Fatigue analysis using CAE methodology can be facilitated with the integration of real load data and prediction. Obtaining load data can be done through measurements or simulations, and it is crucial to integrate this data with the geometry for an accurate analysis of resistance and durability.

Load prediction can be simplified by integrating the data stream into Simcenter 3D Motion, enabling a complete durability analysis when selecting the component and running load prediction.

Benefits:
Direct import of Simcenter 3D Motion results
Typical industry load data formats supported
Superposition of hundreds of measured or simulated load channels and finite element results
Complex Work Cycles
The analysis of specific events, such as torsion or screwing modes, can be done directly from the finite element results, considering the nonlinearity of the material and/or geometry.
FE Result
For cargo acquisition (or third party forecast):
Opening for file formats, load time history and FE
Smart interface to automatically connect channels and load cases
Static and pre-stress cases
Automatically adapt to re-calculations

For components subjected to frequency loads, such as batteries, simulation of random and harmonic events is essential to cover all load conditions.
Efficiently combining these events into a work cycle is facilitated by Simcenter 3D, allowing the creation and activation of load events directly in the graphical interface or from a spreadsheet.
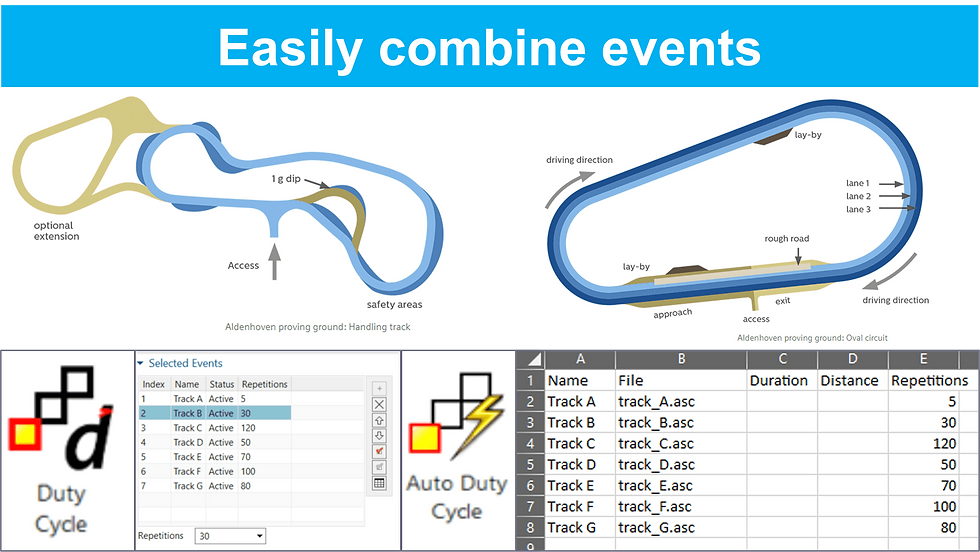
Simcenter 3D 3D Job Cycle Events :
Combine any of the load events
Create in the GUI or automatically from a spreadsheet
Simple activation/deactivation (also from a spreadsheet)
Event Order: Choose to count event order or ignore it
Integration of material data into FE models is simplified in Simcenter 3D, allowing you to inherit material properties or use estimation tools. Advanced methods consider local influences and manufacturing processes.
1. Integration into FE: Inherit material from FE

2. If FE materials do not include fatigue data: Use estimation tools – reusing E, Rm if available.

3. Alternatively, use material from the material database, especially for welding.
Add materials based on FE configuration
4. Double-check by plotting the data
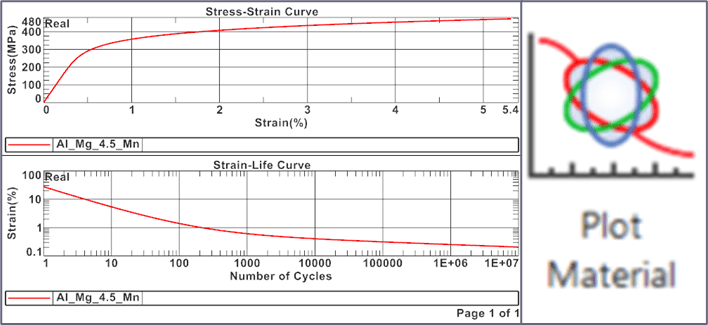
5. Repeat for each material (if inherited, this is done automatically)
To configure fatigue analysis effectively, it is essential to logically group parameters into simulation objects, using templates that guarantee the consistency and robustness of the process. The use of intelligent solvers that select the best methods based on available data is essential.
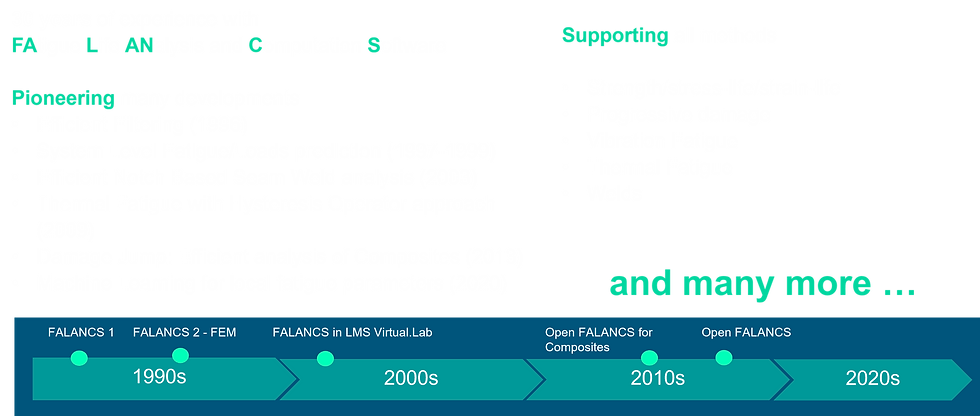
Post-processing of Results
Understanding the results of fatigue analysis is crucial to identifying the causes of failures and improving design. Advanced tools allow you to analyze work cycles in detail, identify critical areas and correlate simulations with real tests. Intelligent local analysis helps reduce loads and improve the flow of loads in the system.

Using this integrated and simplified approach to fatigue analysis, you can perform faster and more accurate design optimizations, ensuring better understanding and continuous product improvement.
To ensure the durability and resistance of components in general, CAEXPERTS offers an advanced CAE fatigue analysis methodology for design optimization and virtual validation. Integrating real load data and simulations, simplifying durability analysis and facilitating accurate load prediction. Schedule a meeting with CAEXPERTS to find out how we can help transform your analysis processes and ensure more robust and efficient results for your projects.
Comments