How to obtain better boundary conditions for engine models?
- Alvaro Filho
- Mar 14, 2024
- 6 min read

The whole engine model (WEM) can be used in the gas turbine industry to accurately calculate the transient thermomechanical behavior of a gas turbine engine under a wide range of operating scenarios. This has clear implications for the service life of the different engine components, as well as the performance and efficiency of the gas turbine itself. But how can we be confident in what we are calculating?
Like any simulation tool, if the inputs are bad, we shouldn't expect much from the results. So how can we ensure our contributions are of the highest fidelity?
Gas turbine Original Equipment Manufacturers (OEMs) have generated a great deal of knowledge and understanding of their respective engines over the years through extensive simulations, trial and error, and test or validation campaigns. The steady state or baseload/navigation status of an engine is critical to understanding engine performance. However, the challenge is how the engine got to this state: what kind of temperature loads and gradients did the metals experience to get to this steady-state condition. To understand this, heat transfer coefficients (HTCs), fluid temperatures and thermal fluxes are critical information to construct and understand the evolution of the gas turbine thermal state throughout an operational scenario.
By capturing the status quo
The following Figure is an example of a thermal boundary condition input window for the turbine specific flow boundary condition.

Example of thermal flux boundary condition input menu.
This is where companies can capture proprietary knowledge of their engine: how flow temperature and pressure evolve as the gas turbine ramps up, reaches base load/cruise speed and altitude, and subsequent deceleration or landing. A crucial input to metal temperature calculation is the heat transfer coefficient: the factor behind the metal temperature evolution through which this boundary condition is placed. In the simple example above, 200 W/m 2•C° is chosen. In reality, as the main physical parameters of the convection fluid (pressure, flow and temperature) evolve throughout engine operation, it is pertinent to take into account the physical changes involved. Below a certain rotational speed, the flow is not transmitted through the motor, which can lead to a different heat transfer process.
The entire engine modeling process can explain this phenomenon under boundary conditions in two ways (see Figure below):
Incorporation of if/then statements into boundary conditions input fields;
Links to key mission/operational cycle parameters that evolve over time.

Example of using conditional statements in gas turbine boundary conditions.
In addition to the above possibilities, typical heat transfer correlations such as the flat-plate correlation, the Nunner correlation, the Dittus-Boelter equation or some derivative thereof can be included as time-varying or window-input equations. input of heat transfer correlation. It should be noted that companies are able to write company-specific plug-ins that contain proprietary knowledge and information that can be called into Simcenter 3D. This user-defined plug-in function is a feature that allows Simcenter 3D users to utilize its proprietary correlations in modeling the physics of their simulation. Users can code correlations in C++ using application programming interface (API) functions that give access to quantities calculated by the solver. These correlations can be used later in Simcenter 3D when applying and defining boundary conditions. The solver will calculate user-defined functions used in expressions, such as heat transfer correlations, during the solve time.
Gas turbines typically have cooling holes for the hottest turbine components or to direct compressor flow into the internal cavities of a rotor. Energy can be transferred to the fluid from such configurations. Windage can be defined as that component of energy that is transmitted from a rotor to the fluid. Simcenter 3D has two dedicated functions that can account for this extra power:
Windage for inclined and vertical surfaces;
Windage for horizontal cylinders.
However, what happens when there is a new gas turbine engine configuration or when the OEM is at the beginning of the design phase of a gas turbine engine where only sketches or operational scenarios are known?
Systems engineering: precision and speed
This is where a systems engineering tool such as Simcenter Amesim or Simcenter Flomaster is often employed by OEMs to define the main operation of the gas turbine before any computer-aided design (CAD) data is available. These types of models built using existing component libraries in the software are flexible and typically mature with the design as it evolves.
In the case of the gas turbine, being able to model and characterize the secondary airflows in and around the gas turbine is critical to understanding the performance and efficiency of the entire engine. Secondary airflow is the portion of the airflow removed from the hot gas path at various stages of the compressor and used for cooling or sealing in the hottest parts of the turbine section. This air needs to be used efficiently and optimally to minimize the impact on engine performance metrics. Simcenter Flomaster has a dedicated library and set of solvers for such simulations. Important physical information, such as swirl correlations relevant to the cavities within a gas turbine, can be calculated and subsequently used as input into boundary conditions throughout the engine model (see Figure below). Similar to WEM's practice of incorporating in-house knowledge and experience, Simcenter Flomaster offers templates for vortex correlations, allowing companies to tailor the solution to reflect their best practices and methodologies. Simcenter Flomaster also contains scripting capabilities so that an enterprise can incorporate its own correlations into the system-level model.

Model of part of the secondary air flow system of a gas turbine.
These types of system-level models can provide advance information about the operation of a gas turbine engine, and the parameters calculated from the model can be used to tailor the heat transfer correlations of the entire engine model. This type of loose coupling can also be extended where the backlash or deformation calculated from the MAE can be fed back into the systems model, allowing the engineer to understand this effect on the network flow distribution. This approach is also relevant for simulating and understanding the performance of labyrinth seals, typically employed throughout the engine to seal air and hot gas from the metal.
Capturing 3D flow phenomena for the 2D world
A second source of input for all engine model boundary conditions is computational fluid dynamics (CFD). Using CFD on the complete gas turbine is prohibitively expensive, despite recent advances in hardware and solver speed. However, it can still be used to better understand local conditions and add more fidelity to the entire engine model. There are a few ways to use CFD in MAE, but first, let's see what CFD can elucidate for a full engine model engineer looking at the gas turbine.
A gas turbine contains numerous areas of forced convection, not just the hot gas path. It is in these other locations that more information can be derived from CFD to better understand the local flow and heat transfer conditions within a gas turbine; locations such as external extraction cavities, cooling holes within a rotor, or purge streams used to minimize or prevent hot gas ingestion. These conditions could also be simulated and understood at times other than steady-state flow, where local HTCs can have a significant effect on heat transfer to and from the metal.


CFD is a valuable tool for understanding local heat transfer conditions within the gas turbine engine.
A full engine model engineer can incorporate a speed-controlled HTC into their model, at thermal boundary conditions, or by directly calculating the HTC from a conjugate heat transfer simulation in a tool such as Simcenter STAR-CCM+.
A second source of CFD input that can be utilized throughout the engine model is to add fluid domains directly into the 2D WEM. Since Simcenter 3D 2022, 3D fluid domains can be included in the axisymmetric part of the entire engine model (see Figure below).
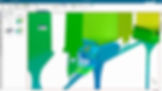
3D fluid domains within the 2D axisymmetric model of the entire engine to simulate air and heat transfer within the cavities between the turbine blades.
This area can be particularly sensitive to temperature changes that can occur due to hot gas ingestion and adversely affect the mechanical life of the spruces.
As we have seen, there are several ways to help you fill in the boundary conditions for your entire engine model. Depending on where you are in the development cycle, different levels of input fidelity can be used to help you better understand your engine's performance and the subsequent impact on your engine's metal temperatures and clearances.
To ensure your engine model achieves maximum accuracy and effectiveness, schedule a meeting with the experts at CAEXPERTS now. Our team can help you understand and optimize your boundary condition inputs, utilizing industry best practices and customized solutions to meet your specific needs. Don't leave the quality of your results to chance - contact us and take your engine modeling to the next level!