
After successfully using Simcenter 3D Smart Virtual Sensing to predict loads for strength and fatigue analysis by combining testing and simulation, the well-integrated workflow optimized the efficiency of the entire team. This approach also included the possibility of “measuring the unmeasurable” on a larger scale.
Challenges in durability analysis
When analyzing potential damage under all possible load scenarios to validate a design, it is essential to obtain accurate data on operational loads. For those who are not experts in durability analysis, designing and validating mechanical structures under static and dynamic loads can be challenging, especially when trying to include operational loads in the study.
With smart virtual sensing, operational loads can be obtained for durability analysis. The resulting information on remaining service life is extremely valuable. Despite the specialized tools available for detailed analysis, there is also a need for simpler and more integrated methods for everyday use.
The old problem
Traditionally, strain gauges are installed on prototypes to perform durability and validation testing. The big challenge is not that critical damage often occurs in areas where it is difficult or impossible to obtain direct formation effects due to geometry limitations.
A new approach
For load prediction, Simcenter 3D Smart Virtual Sensing can use just a few strain gauges in easily accessible locations to predict operational loads. The question was: could this approach be used continuously to measure unmeasurable loads and predict structural failures?
Simcenter 3D Smart Virtual Sensing 2412 is dynamic and has a new feature – the Virtual Damage Sensor. This feature improves structural failure detection, providing a practical solution to a recurring problem.
Solution Implementation
With the Smart Virtual Damage Sensor solution, strain gauges can be placed in accessible locations to provide the smart virtual sensing tool with the necessary data. This enables data fusion between the physical measurement and the FE model, providing measurements in locations that are difficult to physically measure. Virtual sensors provide detailed results, including strain, stress, velocity, and displacement.
In addition, the newly added virtual sensors integrate virtual sensing with durability analysis to provide important damage information, such as remaining service life, accumulated damage history, and damage increments. When combined, these results provide insights into the durability of the structure, indicating when damage is likely to occur and how much useful life is left.
The workflow
The process for implementing this solution follows these steps:

Step 1:
Use Simcenter 3D Smart Virtual Sensing Optimal Sensor Placement to determine where to place the physical strain gauges
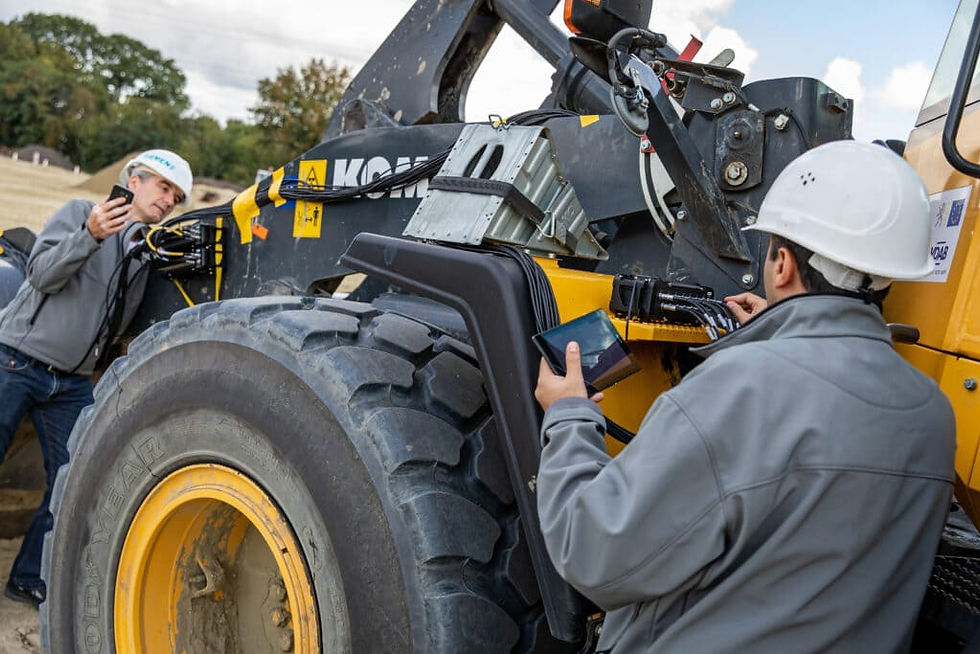
Step 2:
Perform physical testing using Simcenter SCADAS and obtain strain measurements with operational loads.
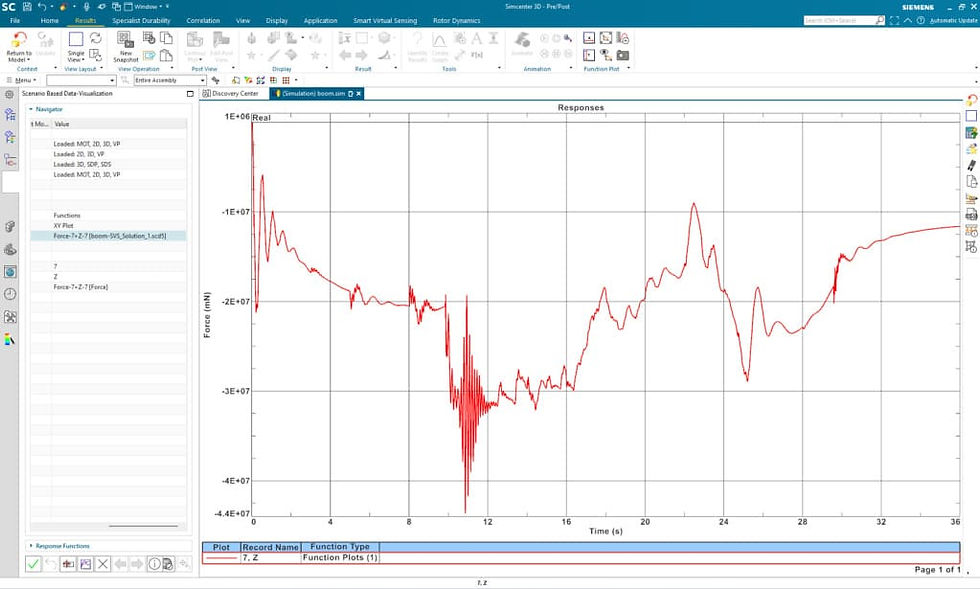
Step 3:
Predict operational loads by feeding the measurements and the reduced-order finite element model into Simcenter 3D Smart Virtual Sensing.

Step 4:
Complete the durability study in Specialist Durability by connecting it to the Smart Virtual Sensing events.

Step 5:
Perform a durability study and figure out where the potential damage area is. (Step 4 and 5 are a recommended but optional way to find the critical areas).

Step 6:
Put virtual damage sensors on the potential damage area and run the smart virtual sensing solution to get damage information in the selected locations
The results
With this workflow, data on remaining useful life, accumulated damage history, and damage increments can be obtained, allowing for more accurate analysis of the root cause of damage.
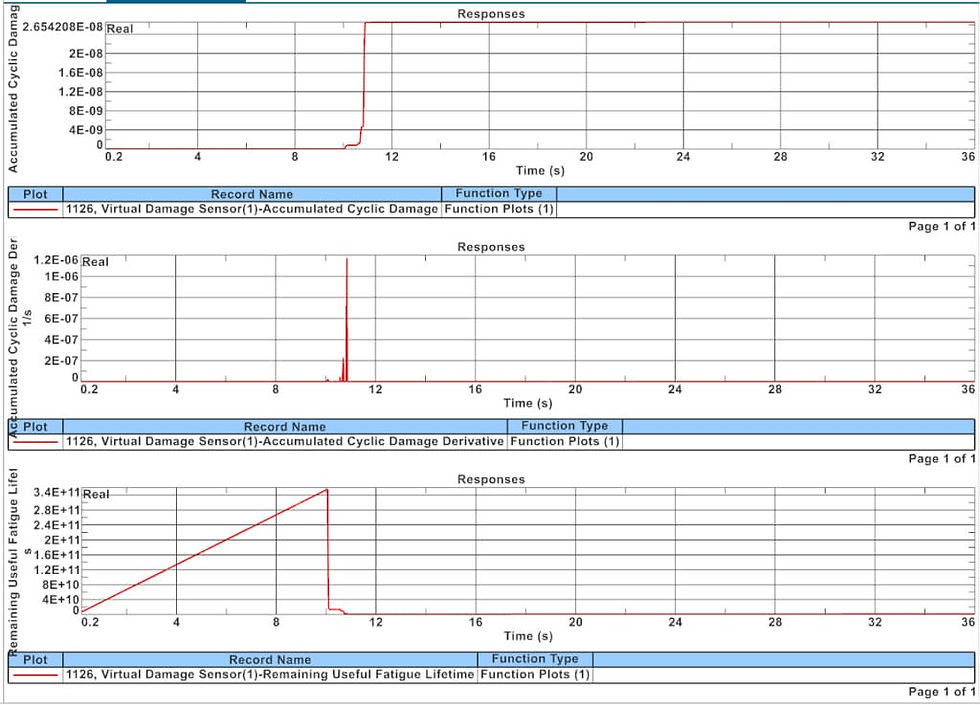
By following this process, structural damage analysis becomes more efficient and reliable. The Smart Virtual Damage Sensor is a valuable tool for design and validation, offering a practical way to measure damage and assess remaining service life at critical locations.
In addition, by making the Virtual Damage Sensor a real-time solution, it is also possible to implement predictive maintenance. This allows potential problems to be identified before they occur, avoiding costly downtime. Optimizing maintenance task scheduling can reduce large safety factors typically included in worst-case scenarios, making structural engineering more accurate and cost-effective.
Schedule a meeting with CAEXPERTS and find out how the Simcenter 3D Virtual Damage Sensor can transform your durability analysis, making it more accurate and efficient. Talk to our experts and take your structural engineering to the next level!
WhatsApp: +55 (48) 98814-4798
E-mail: contato@caexperts.com.br
Comments