Success Story: CFD Simulation in Boiler Optimization
- Alvaro Filho
- Apr 8
- 4 min read
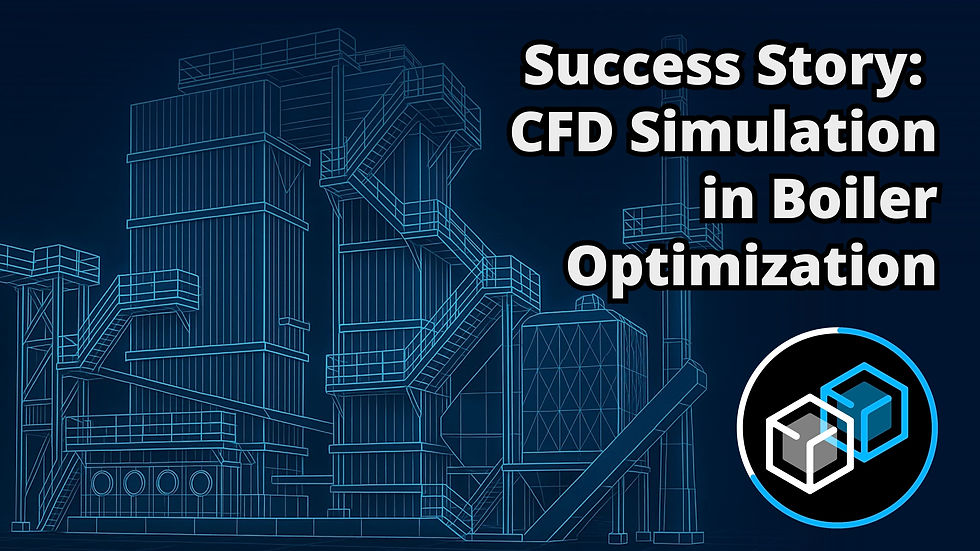
In the modern power generation industry, where competitiveness demands operational excellence, the efficiency of industrial boilers stands out as a crucial pillar for success. Designed to meet performance and sustainability demands, these systems prioritize parameters that aim to: maximize the useful life of boilers and piping, optimize thermal efficiency, reduce emissions and ensure energy generation at maximum levels.

In this scenario, furnaces emerge as a reference technology. Their differential lies in the arrangement of independent flames, which ensure stable combustion even under minimum operating loads - a critical advantage in scenarios of variable demand. In addition, their versatile architecture is not restricted to the traditional boiler format, allowing adaptations to different projects without compromising efficiency. Another highlight is the ability to maintain minimum deviations in the temperature of fuel gases along the horizontal flow, ensuring homogeneous thermal distribution and reducing the risk of premature degradation of components.
Challenges and Solutions
In the search for efficient combustion and reactive flow systems, the technical challenges transcend specific applications, focusing on four essential pillars: reducing pollutant emissions, maximizing energy efficiency, controlling costs (both design and maintenance) and adopting technological innovations, such as alternative fuels, hybrid systems and advanced materials.
The strategic solution to these challenges lies in the creation of digital twins – virtual models that simulate real processes with high precision. In practice, companies use these simulations to optimize flame dynamics, heat transfer, thermal wear resistance and emission control (NOx, soot, CO). Furthermore, in complex reactive systems, predictive analyses allow for the prediction of critical parameters such as yield, chemical conversion, product selectivity and undesirable operating conditions, such as hotspots or stagnation zones.
CFD simulation with STAR-CCM+ stands out as a strategic tool in this context, enabling the modeling of complex phenomena. Design variants can be quickly explored from the initial phases. This includes everything from adjustments to flame geometry and thermal distribution to the integration of new operating strategies.
Simulation
The simulation study, using STAR-CCM+, in question focuses on the detailed analysis of the furnace of an industrial boiler, with the aim of investigating the combustion characteristics of natural gas and its impact on the efficiency and operational stability of the equipment.
The simulation was developed based on a non-premixed combustion model, incorporating the detailed chemical kinetics of natural gas through a kinetic mechanism with more than 400 reactions. The computational mesh was strategically refined in critical regions, such as the flame zone and gas outlets, while the boundary conditions replicated real operational scenarios, including proportional fuel and oxidizer input.
Figure 1: Geometry and computational mesh
The results in Figure 2 show the temperature distribution in the furnace, where the regions close to the central line of the gas flow reach temperatures above 2000 K, indicating intense combustion activity. However, a low temperature zone is observed near the burner nozzles, caused by the high concentration of air in these areas, which dilutes the fuel mixture and reduces local thermal efficiency. Measuring this inefficiency is essential to verify whether the cost of preheating is justifiable or not, for example.
Figure 2: Temperature profile
From the image of the temperature field above, it is possible to understand the thermal distribution of the boiler and determine whether the areas of interest are at the appropriate temperature and receiving sufficient heat.
Figure 3 shows the concentration profiles of CO₂, CO and OH along the height of the boiler. The CO₂ concentration increases progressively as the gases rise, reflecting the complete oxidation of the fuel in contact with the available oxygen. CO, on the other hand, shows peaks close to the burners, resulting from the centralized injection of methane (CH₄) combined with insufficient air in the primary zone. As the gases rise, CO is converted to CO₂ due to the greater availability of oxygen. The OH profile, in turn, confirms the stability of the flame, with high concentrations in regions of intense combustion, signaling combustion efficiency.
Figure 3: Concentration profiles: (a) CO₂; (b) C; (c) OH
In Figure 4, the velocity field and streamlines reveal how the geometry of the furnace and burners influence the flow of gases. Recirculation zones below the burners stand out, which retain unburned particles and improve combustion efficiency, and "dead" spots (regions of low turbulence), where there is a risk of accumulation of unreacted material. These patterns highlight the need for adjustments in the geometry to optimize the flow and avoid energy losses.
Figure 4: Velocity profile
Technical implications
The results highlight opportunities to improve furnace design:
Adjust the air-fuel ratio in the nozzles to reduce low-temperature zones.
Redesign the geometry to minimize dead spots and ensure homogeneous flow.
Improve the fuel-air mixture to control CO emissions as well as NOx and SOx.
Evaluate fuel substitution (heavy oils, for example, for natural gas).
Success story: How Suzano, in partnership with the Sector University and ABTCP, optimized lime kilns with digital technology from Siemens STAR-CCM+

Suzano, in collaboration with the Sector University and ABTCP, transformed operational challenges into significant results using digital twins and computer simulations (CFD). The lime kilns faced recurring burner obstructions, high natural gas (NG) consumption and variability in carbonate, interrupting operations every 19 days.

Using STAR-CCM+ software, the team adjusted primary (20%) and radial (30%) air ratios, implemented central air (7.5 m/s), and redirected the methanol spray. The results were astonishing: 7% reduction in NG consumption, 29% less carbonate and 160+ days of continuous operation without clogging, plus stable bed temperature (1020°C).

The case reinforces the power of digitalization in the industry: efficiency, sustainability and productivity go hand in hand when innovation and strategic partnerships come together.
Conclusion
The optimization of industrial boilers and furnaces through computer simulations, such as those performed with STAR-CCM+, has proven to be a way to overcome the challenges of the modern energy industry. The use of simulations, as in the case of Suzano, shows that digital technology improves performance, reduces emissions and increases the useful life of equipment. Investing in these solutions is a sure path to greater sustainability and productivity.
Schedule a meeting with CAEXPERTS and discover how computer simulation can transform your industrial processes, optimizing efficiency, reducing emissions and extending the life of your equipment. With STAR-CCM+, you can implement customized solutions for real challenges. Talk to our experts and take your operation to the next level!
WhatsApp: +55 (48) 98814-4798
E-mail: contato@caexperts.com.br
Comments